The variety of industrial applications that can be supported through the use of Ethernet technology continues to expand as the “Internet of Things” evolves into the “Industrial Internet of Things” and organizations work to improve operations through data integration. The networking requirements for applications can vary widely and most industrial networks will need to support a mix of Fast Ethernet (100Base) and Gigabit Ethernet (1000Base), or GigE, devices in the near future. After providing a foundation of industrial networking basics, this white paper will discuss when to choose GigE over Fast Ethernet through a series of application examples.
Introduction
.jpg)
Today’s industrial networks are managing increased data flow from sensors and video monitoring systems, integrating processes to include M2M monitoring and seamlessly sharing data between facilities in real time to synchronize operations. As a result, industrial organizations investing in the value of the connected facility are now wondering how much longer their networks will be able to keep up with demand. They face the ongoing challenge of allocating and scaling bandwidth to support all of these new functions, along with what’s coming next as the “Internet of Things” and concepts like the “Connected Factory” and “Industry 4.0” become more widespread.
Industrial networks will need to support a mix of Fast Ethernet (100Base) and Gigabit Ethernet (1000Base), or GigE, devices in the near future. Fast Ethernet provides outstanding performance for many industrial control and remote monitoring applications. It’s also the common network connection built into many leading HMIs, controllers, sensors and other industrial automation equipment. However, video transmitted over Fast Ethernet tends to be choppy, and the bandwidth is insufficient for high-speed motion control and other applications that require low-latency networks. That’s where the power of Gigabit comes in for today’s industrial networks. After providing a foundation of industrial networking basics, this white paper will discuss when to choose GigE over Fast Ethernet through a series of application examples.
Industrial Networking Basics
Industrial networking is in the middle of two simultaneous transitions. First, Ethernet-based protocols continue to displace older fieldbus technologies. Ease of deployment and interoperability is a major reason Ethernet has become so popular for networking in industrial and remote operations – EtherNet/IP, Modbus TCP/IP, PROFINET, DeviceNet and other popular protocols are all Ethernet based. As these networks continue to grow, a second transition is underway to increase bandwidth and reduce latency through Gigabit Ethernet technology.
Ethernet has become widely accepted and installed because of its speed, reliability and support as an international standard. Industrial Ethernet networks typically use 100Base Fast Ethernet technology with 100 megabits per second (Mbps) bandwidth that can also support older 10 Mbps (10Base) Ethernet devices, and thus is referred to as 10/100 technology.
Gigabit Ethernet is 1000Base. By definition it provides 10 to 100 times the bandwidth of the 10/100 Base networks that are installed in many facilities today. The increased bandwidth enables larger networks to transmit data more quickly and also allows the network to carry larger data files (for example, higher-resolution images) without experiencing quality-of-service or performance issues.
Gigabit Ethernet also has lower switch latency than earlier-generation technology, which may be more important than speed for industrial control operations. Switch latency refers to the time required for a packet to enter and exit a network switch. Reduced latency is a welcome enhancement for highly sensitive motion control systems. Gigabit Ethernet and Fast Ethernet are both full-duplex protocols, which mean they can send and receive simultaneously.
When to Choose Gigabit over Fast Ethernet
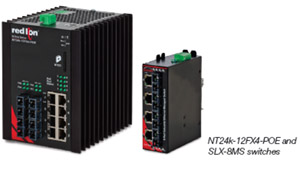
Enterprises will likely need to support a mix of Fast Ethernet and GigE devices in the near future. Fast Ethernet provides outstanding performance for many industrial control and remote monitoring applications and is the network connection built into many leading HMIs, controllers, sensors and other industrial automation equipment. These devices were developed to transmit limited data and may not be optimized to support the data, voice and video traffic that typically flow over modern networks. Video streams transmitted over Fast Ethernet tend to be choppy. Bandwidth is also insufficient for high-speed motion control and other applications that require minimal latency. Because Fast Ethernet and GigE can coexist, enterprises should develop a flexible network backbone that can readily support both technologies. Enterprises can achieve the flexibility to bridge current and future requirements by using network switches that support different protocols, media types and modules. For example, the N-Tron® series NT24k managed switches from Red Lion Controls offer up to 24 ports that support a mix of GigE and Fast Ethernet, copper and fiber, and are configurable to work with different protocols, network architectures and modules.
Forward and backward capability is one of the key advantages supported in the Ethernet standard family (IEEE 802.3 standards). Gigabit Ethernet, Fast Ethernet and 10 Mbps Ethernet devices can all be used together on the same network. With proper planning, Gigabit Ethernet can be strategically deployed and will provide a seamless upgrade path while preserving previous investments in devices and network administration expertise.
Gigabit Ethernet Applications
Organizations are making the decision to upgrade to GigE because they want to future-proof their networks to accommodate more traffic and next-generation devices and applications. A few application examples follow:
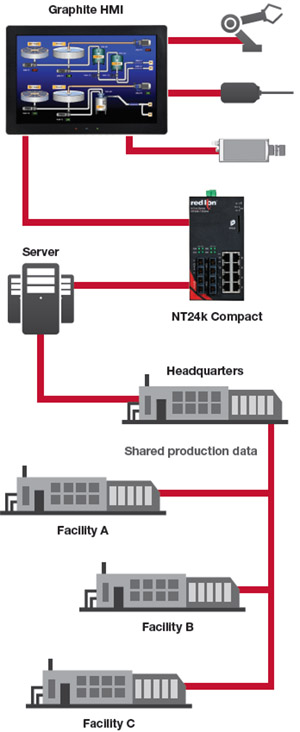
Video Cameras
Video is becoming increasingly important for facility management and production control operations. There is growing demand for traditional surveillance, but many new and powerful use cases are also emerging. For example, video cameras are being installed on wind turbines to enable remote inspection. If the turbine performance changes suddenly or an alert is generated, a technician hundreds of miles away can use the camera to inspect the turbine for damage. This can save time and money by eliminating expensive field service calls. If on-site service is needed, technicians can use video footage to help diagnose the problem so they can bring the right tools and materials to fix the problem on the first visit.
Low-cost closed circuit surveillance cameras do not provide the image quality needed for remote monitoring or parts and assembly inspection. These applications require better quality images, and a higher-capacity network to carry them. Typical surveillance systems use cameras that capture from one frame per second (fps) up to 29 fps, though many industrial applications operate at 10 fps or less. Machine vision cameras used for part identification and assembly verification may run at 48 fps and have more megapixels, or resolution, to create higher-quality images. The combination of higher speed and higher quality results in inspection applications requiring much more bandwidth than traditional surveillance systems. Cameras used for intelligent highway systems and to monitor rolling stock typically have speeds and resolutions somewhere in between those used for inspection and basic surveillance.
Surveillance applications can also benefit from Gigabit Ethernet connectivity because it has the bandwidth to support higher resolution images, better motion quality and enables more cameras to be used without negatively impacting network performance. For example, intelligent highway systems benefit from having input from many locations, but operating statewide camera infrastructures requires high availability and high bandwidth networks. These requirements fully support the deployment of a Gigabit Ethernet backbone.
Larger-Population Networks
All signs point to more connectivity in future field and factory operations. There have been numerous studies and forecasts predicting explosive growth for M2M, the Internet of Things and industrial networking. Industry leaders have predicted the number of networked devices will double to 50 billion between 2015 and 2020. Much of this increased connectivity will occur in the industrial space in the form of sensors and M2M devices, based on current automation trends and the high percentage of OEMs that are building M2M capabilities into product offerings.
Workstations that currently include a few devices connected to an HMI in an isolated ring network will likely evolve. Soon, a work-station may interface with dozens of sensors that support robotic production equipment, with each component reporting its status and production data to the cloud. Not only will there be more networked devices in the future, the devices will share more data and have more interactions with other systems. These developments underscore the need for network infrastructure that can support both Gigabit Ethernet and older technology, while providing enough ports to support multiple devices.
Facility-to-Facility Connectivity
Industrial networks increasingly are links in a network of networks that make real-time data available throughout the extended enterprise. Remote cameras on wind turbines or oil wells may be monitored by a technician thousands of miles away. Data from sensors, RTUs and other devices that are spread out over several acres at a manufacturing facility might continually report equipment status conditions to feed centralized production management and maintenance systems. In this scenario, Fast Ethernet or fieldbus protocols may be sufficient for devices at the local level, while Gigabit Ethernet provides the network backbone for communicating with other buildings and remote locations.
Industrial facilities are quickly becoming dynamic, networked environments that enable enterprises to connect, monitor and control their assets remotely. However, these changes won’t occur all at once, so organizations must plan to continue supporting current systems while building for the future. The components to create the connected enterprise are available now, and the evolution can take place as quickly as network bandwidth allows. GigE offers the bridge that businesses need to construct high-capacity industrial networks that not only meet today’s requirements, but will also easily support additional video, sensors, M2M and connected devices tomorrow.
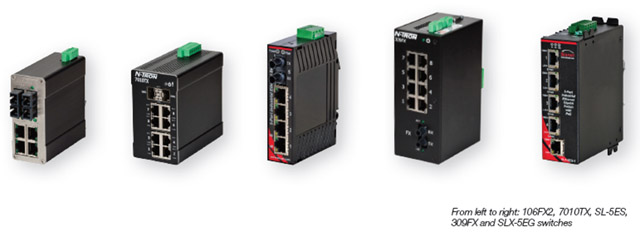
Future Needs: Flexible, Modular Solutions
As different parts of factories, wind farms and upstream and downstream oil and gas facilities connect to each other and to the cloud, the islands of automation that marked earlier-generation industrial automation systems will disappear. They will eventually be replaced by networked environments that enable enterprises to connect, monitor and control their assets remotely. These changes won’t occur all at once, so enterprises will need to support current systems while building for the future. The components to create the connected enterprise are available now, and the evolution can take place as quickly as network bandwidth allows. Gigabit Ethernet is the bridge that enterprises can use to build networks today to pave the way to bring more video, sensors, M2M and other connected devices into their operations tomorrow.
Red Lion provides industrial Ethernet switches that combine high performance with rugged reliability to provide a “best of both worlds” solution for many of today’s industrial applications. Our N-Tron and Sixnet® series of hardened switches are ideally suited for harsh and outdoor environments that include alternative energy, power substations, oil and gas, transportation and other industries where real-time performance under extreme operating conditions is required. Many of our industrial networking solutions support a mix of GigE and Fast Ethernet, copper and fiber, and are configurable to work with different protocols, network architectures and modules. Built-in redundancy coupled with advanced security and network management ensures the infrastructure stays up and running while providing tools for monitoring and tracking.